- Room 1807, Unit 9, Building 2, Shangxing Commercial Street, Shangde Road, Shangxing Community, Xinqiao Subdistrict, Bao'an District, Shenzhen City, China
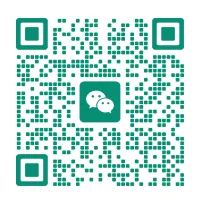
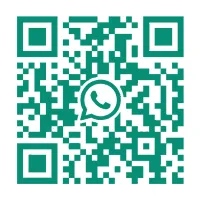
Aerospace & UAV
WJ Prototypes is your 3D manufacturing partner from prototype to large scale production.
Consumer Electronics
New Product Introduction Solutions for Consumer Electronics.
Robotics & Automation
Need some assistance bringing your robotic device or parts from the sketch-board to reality?
Medical Devices
The medical industry needs high quality, dependable and safe parts and products.
Automotive
New Product Introduction Solutions for Automotive
Industrial Machinery
The main purpose of industrial prototyping is to take the product from drawings into the real world.
Manufacturing in China remains a cornerstone of global industry, even amid shifting U.S. tariff policy. For example, China’s massive port infrastructure (shown below) reflects its role as the world’s factory. Its share of global manufacturing output has climbed from just 6% in 2000 to roughly 31% today, dwarfing other nations. China’s factories produce everything from electronics to textiles underpinned by sophisticated supply chains. Yet recent U.S. policy changes have dramatically raised import duties: by mid-2025 bilateral tariffs on Chinese goods had spiked to well over 100% before a temporary truce cut rates back down to about 10%. Understanding these tariff moves is crucial for manufacturers and procurement managers, because each adjustment can quickly raise costs or shift market demand. Studies show that the 2018–19 tariffs disrupted global supply chains, raised U.S. input costs and consumer prices, and prompted companies to rethink sourcing. In short, tariffs act like taxes on import prices, and even a 10–20% hike can cut deeply into profit margins or force higher retail prices. Manufacturers and supply-chain professionals need to adapt their strategies to these dynamics.
China’s manufacturing might is unparalleled. It contributes nearly 30% of China’s GDP and over 30% of world manufacturing output. According to UN data, China’s global output share rose from 6% (in 2000) to 31% in 2024, and is projected to reach 45% by 2030. Its factories churn out a vast range of products (from smartphones to heavy machinery) with remarkable scale and efficiency. China excels especially in technology-intensive sectors: for example, it leads or is on par with global leaders in electric vehicles, batteries and nuclear power. Meanwhile, China’s labor pool and supplier networks allow it to produce large volumes cheaply. As one analysis notes, China provides “efficiency: robust infrastructure, skilled labor and streamlined logistics,” along with “scale: vast capacity” and “integration: highly integrated supply chains”. These advantages help Chinese factories offer competitive pricing, making them hard to replace. In practice, U.S. firms still rely on China for key parts and assemblies in electronics, automotive, aerospace and other fields. Thus, any tariff on Chinese goods has ripple effects on global manufacturing costs and supply chains.
A tariff is simply a tax on imported goods. When a government imposes a tariff, the foreign-made product becomes more expensive for domestic buyers. Tariffs are often intended to protect local industries or raise revenue, but in practice they “increase the price of goods from another country, making them less attractive”. For example, a 25% tariff on imported bicycles means each bicycle costs 25% more at the border, so U.S. consumers see higher prices or buy alternatives. In many cases, studies find that 80–100% of a tariff is passed through into higher U.S. prices. In short, a tariff is not paid by foreign exporters – it is borne by whoever pays for the goods (importers, wholesalers, or end users).
U.S. tariff policy toward China has shifted repeatedly in recent years. Starting in 2018, the Trump administration launched a broad trade war: it imposed 25% tariffs on steel and aluminum (Section 232 measures), then proceeded to levy 10–25% tariffs on hundreds of billions of dollars of Chinese products under Section 301. By late 2019 about $370 billion of Chinese goods were covered by U.S. tariffs (25% or higher). In September 2024, the U.S. completed a four-year “Section 301” review and announced new duties of 25–100% on 14 categories of Chinese imports (ranging from machinery to auto parts). Most recently, in early 2025 the U.S. imposed a 20% tariff on virtually all Chinese imports. These layers of duties mean that, at one point, U.S. tariffs on Chinese imports averaged well over 100% (factoring in multiple tariffs). In mid-2025 a meeting in Geneva led both sides to temporarily reduce tariffs to about 10% each, but those cuts last only 90 days. In summary, the U.S. now enforces much higher duties on Chinese electronics, machinery, and consumer products than were in place before 2018. (For reference, as of June 2025 the U.S. average tariff on Chinese exports stood around 51%, down from a peak of ~126% earlier in 2025.)
Tariffs affect both producers and buyers. Empirical research finds that each 10 percentage points of tariff increase typically raises U.S. import prices by about 1%. Thus the 21-point tariff jump of 2018–19 corresponded to roughly a 21% rise in the price of Chinese imports in the U.S. market. In practice, most of this extra cost has been borne by American businesses and consumers. For example, U.S. retailers and manufacturers have reported higher input costs and have often passed these increases along to customers. In effect, tariffs operate like a hidden sales tax: if a Chinese-made component costs $100, a 20% tariff makes it at least $120, so either U.S. firms pay more or consumers do.
On the manufacturing side, higher U.S. tariffs create uncertainty. The 2018–19 tariff surge, for instance, caused many companies to reconfigure their supply chains. A Federal Reserve analysis found that dozens of U.S. firms shifted production from China to countries like Mexico or Vietnam to avoid the highest duties. Meanwhile, firms that remained exposed warned that it was hard to predict final costs, and 72% of S&P 500 companies mentioned tariffs in early 2025 earnings calls. In practice, analysts note that many businesses are “strengthening supply chains” and “boosting near-shoring” efforts in response. This means the tariff changes have not led to a straightforward resurrection of American manufacturing; instead they have triggered global supply-chain shifts. In international relations, such tit-for-tat tariffs strain trade ties. China responded to U.S. duties by raising its own tariffs on American goods (peaking at ~147% on average before the 2025 truce). Ongoing tariff adjustments thus inject volatility into trade relations: companies and governments must continually adapt to changing border tax policies, or risk losing market share and efficiency.
China’s factories today blend scale with increasing sophistication. The country leads the world in many high-tech manufacturing areas. For example, China dominates global production of electric vehicles, batteries, solar panels and telecommunications equipment. Its “Made in China 2025” initiative explicitly targets advanced sectors like aerospace, robotics and biopharma. Chinese firms have invested heavily in automation and smart manufacturing: one report notes Chinese manufacturers are incorporating Industry 4.0 technologies (IoT, AI, robotics) to improve quality and efficiency. Even solar-panel factories use industrial robots for assembly, and Chinese planners emphasize automation over labor-intensive production.
Photo by Hyundai Motor Group
China has long been known as the low-cost producer of basic goods, but it has been moving rapidly up the value chain. According to RAND Corporation analysts, China’s focus today is on manufacturing efficiency — automating and innovating to offset rising wages. Many Chinese state-led efforts (and foreign joint ventures) support cutting-edge R&D; for instance, China now leads or is on par with global leaders in commercial nuclear power and electric vehicles. In markets like electronics, telecommunications and automotive, China not only achieves large output volumes but is increasingly making complex components (microchips, high-speed rail parts, advanced robotics). Its established supply-base and infrastructure – from mega-ports to dedicated industrial parks – remain unmatched in Asia. In short, China’s manufacturing capabilities span low-cost mass production and sophisticated industries.
China’s cost advantage stems from multiple factors. Wages in China, while rising, are still relatively low (in 2020 around $6.50/hour on average) and productivity is high, enabling bulk manufacturing at low per-unit cost. Suppliers, raw materials and logistics are highly concentrated: China’s vast supplier ecosystem means a factory can source components nearby, reducing shipping and inventory costs. Analysts highlight China’s “efficiency” (modern ports and transport, skilled labor) and “scale” (huge workforce and production capacity) as major draws. In practice, this integrated industrial base lets many Chinese manufacturers absorb some of the tariff cost or offer prices that outcompete alternative factories. Safeguard Global notes that China combines “low costs, a large workforce and high production quality”, which together keep Chinese products competitively priced on the world market.
Of course, higher tariffs do chip away at margin: a factory in China must decide whether to absorb a 10–25% increase in costs or pass it on via higher export prices. In response, some Chinese firms have adopted aggressive cost-cutting (leaner operations) and sought economies of scale to maintain competitiveness. Meanwhile, other companies, especially those making higher-value products, emphasize Chinese attributes beyond cost. As one sourcing analysis notes, brands stick with China not just for cheap labor but for its “integration” – i.e. a complete vertical supply chain – and excellent logistics. In other words, firms accept slightly higher tariffs or wages because China’s overall value proposition (speed, reliability, infrastructure) still often beats alternatives. Nevertheless, U.S. tariffs on Chinese inputs do force price adjustments. Importers may have to raise retail prices for goods made in China (passing along the tariff), or they risk eroding suppliers’ profits.
Overcome the tariff changes with expert help. Contact us through our contact us page
OR Email to info@wjprototypes.com
Quality control has become a priority in China’s factories. Today China produces products at virtually every quality level: from inexpensive consumer goods to high-precision aerospace parts. Importantly, many Chinese factories now meet strict international standards (ISO, IATF, etc.) and follow rigorous process controls. Global companies routinely base their high-end production in China. For example, a 2025 industry report highlights that “global giants like Zara and BMW rely on China’s high-quality manufacturers,” and that Tesla’s Shanghai Gigafactory produces over one million vehicles annually to meet demanding safety and quality norms. That report also notes that luxury brands (Armani) and tech leaders (Apple, Tesla) choose Chinese lines for premium products. In short, “Made in China” is no longer synonymous with cheap throwaways – with proper oversight Chinese suppliers can deliver premium quality. Even Safeguard Global acknowledges China’s manufacturing advantage comes with “high production quality” along with low cost. The key for firms is to enforce quality management: most experts recommend detailed specifications and frequent audits to prevent defects (for example, a recent guide on China manufacturing lists audit, specify, control as the three essential steps to ensure quality). When done well, Chinese factories can produce parts and products of precision comparable to any in the world, which is why many OEMs and brands continue to source critical components from China despite tariffs.
When the U.S. imposes a tariff on Chinese-made products, the immediate effect is to raise their import cost. For instance, economists estimate that a 20% tariff on Chinese imports increases the effective cost of those goods by roughly 22%. In practice, this added cost is typically passed along: nearly all studies find a tariff’s burden falls on the domestic buyer. A Federal Reserve review notes that tariff pass-through is often near 100%. In plain terms, when an American company buys a part from China, a higher tariff simply makes the price at the U.S. port that much higher. The importer can either raise prices to customers or eat the tariff by reducing profit. Either way, tariffs squeeze margins or raise consumer prices. Over time, U.S. and foreign businesses have catalogued how tariffs on inputs – steel, electronics components, etc. – have increased assembly costs. For example, automakers report that new U.S. duties on parts make cars more expensive to build. In sum, tariffs directly inflate the cost of Chinese imports, and the usual outcome is that end-users (wholesalers and consumers) pay higher prices.
Faced with higher costs, companies often adjust where and how they manufacture. Many U.S. and global firms have pursued a “China+1” strategy: they keep some production in China (for the local market or to leverage expertise) while diversifying elsewhere. The 2018–19 tariff surge, for example, led numerous manufacturers to expand facilities in Southeast Asia or Mexico to sidestep some duties. A recent Reuters analysis finds that 72% of S&P 500 companies mentioned tariffs in early 2025 earnings calls, and most said they were revising supply chains and pricing in response. Companies from electronics to consumer goods have plans to source components outside China or increase U.S. production capacity in light of the tariffs. On the other hand, some companies maintain or even expand their China footprint to stay cost-competitive. Interact Analysis notes that firms heavily reliant on the Chinese market continue investing there, while others broaden their Asian operations. In other words, many manufacturers are hedging: they may shift some tooling and orders to Vietnam, India or Mexico (to avoid tariffs), but they often keep complex or high-volume work in China. Over the longer term, firms are also looking at technology: U.S. producers may automate more or design products differently to reduce reliance on tariffed imports. In practice, building new factories or lines takes time and capital, so most companies proceed cautiously. However, the message is clear: tariffs have spurred a wave of supply-chain reorganization, with many firms expanding near-shore options and others emphasizing inventory flexibility.
Extended tariffs would certainly pressure China’s export sectors, but analysts believe Chinese manufacturers have levers to adapt. Chinese industry has been on a recovery path: by late 2024, industrial output and domestic consumption were rising steadily. One industry forecast notes that, even after tariffs on electronics and appliances, China’s domestic market and planned stimulus (over $130 billion in spending) should sustain growth. Indeed, the government has signaled plans for targeted support – for example, encouraging equipment upgrades, trade-in programs and subsidies to keep factory orders flowing. These actions are meant to offset any slowdown in exports caused by tariffs.
Chinese firms are also adapting strategically. Many of the country’s leading manufacturers are setting up plants overseas to get around tariffs, while still anchoring core components in China. For example, electric vehicle and battery companies (BYD, CATL) and electronics makers (Luxshare, Goertek) have built production in Southeast Asia and Europe. At the same time, analysts argue that China’s real goal is to move up the value chain. RAND notes that instead of relying on low-cost labor, China is investing in automation and R&D for efficiency. In fact, China’s R&D spending is set to surpass the U.S. by some measures, and its firms are increasingly innovation-driven.
Overcome the tariff changes with expert help. Contact us through our contact us page
OR Email to info@wjprototypes.com
Image by Pete Linforth from Pixabay
In practical terms, prolonged tariffs might slowly erode China’s share of some U.S. markets, but not overnight. Chinese suppliers still benefit from scale, experience and local government backing – qualities hard for competitors to replicate quickly. Many analysts expect China to lean more on its huge home market (diversifying exports to the Global South) and higher-end segments (luxury goods, technology) that are less price-sensitive. Overall, the consensus is that China’s manufacturing will remain dominant, but with more emphasis on innovation and quality as lower-end markets fragment.
Amid high tariffs on China, companies are indeed looking at other countries. Popular alternatives include Vietnam, India, Bangladesh, and for U.S. needs Mexico. For example, Vietnam is often cited as a lower-cost, trade-friendly alternative. Wages there (around $3/hour) are about half of China’s, and Vietnam has signed many free-trade agreements. Big brands (Samsung, Foxconn, Nike) have shifted some production to Vietnam to diversify from China. However, Vietnam has its limits: it has a much smaller labor force and still-developing infrastructure. One industry review warns that “Vietnam’s smaller manpower size… limits its production potential, especially for large-scale manufacturing,” and that many factories still import raw materials from China. In other words, Vietnam can take on some labor-intensive, high-volume work, but it lacks China’s full ecosystem.
India is another target for diversification. It offers a vast workforce and government incentives (e.g. “Make in India”) that are attracting investment in textiles, pharmaceuticals and auto parts. Even Apple and others have begun shifting some output there. But India’s infrastructure remains uneven: major ports are modern, yet inland transport and customs are slow. Analysts note that poor road conditions, regulatory hurdles and bureaucratic customs can lead to long delays. Additionally, while labor is relatively cheap, productivity and supplier networks are still catching up.
Closer to home, Mexico has become an important manufacturing hub due to its proximity to the U.S. market and strong auto/electronics industries. Mexico’s factories offer short lead times for U.S. companies and benefit from trade agreements with North America. But they face their own drawbacks: distances to Asian suppliers remain far, certain regions have security concerns, and labor costs (especially for skilled work) are higher than in Asia.
In short, each alternative has pros and cons compared to China. For example, one analysis observes that China enjoys “advanced” logistics and “highly integrated” supply chains, whereas Vietnam and India are still developing theirs. The bottom line is that no other single country currently matches China’s combination of scale, cost and network effects. Companies should carefully evaluate capabilities versus tariffs: often a mix of China and one or more “plus” countries (a China+1 strategy) is the practical path forward.
The U.S. government has also moved to encourage more domestic production. Legislation like the CHIPS Act and the Inflation Reduction Act provides tax credits and grants to onshore factories in chips, clean energy and critical industries. For instance, the advanced manufacturing production tax credit (Section 45X) offers a 25% credit on qualifying equipment. The Treasury Department notes that such incentives have already spurred huge investments – over $92 billion announced in American clean energy manufacturing facilities alone. These initiatives aim to bring some production back stateside, reducing reliance on imports.
However, high U.S. labor costs mean nearshoring or reshoring has limits. Even global companies admit that building new capacity in America can be expensive. A recent Reuters report points out that moving manufacturing to the U.S. often “will also raise labor costs,” which can offset tariff savings. In short, domestic facilities can improve supply security and create local jobs, but they typically cannot achieve the same low per-unit costs as China. This means many firms continue using China for cost-sensitive components while using U.S. plants for specialized or final assembly. Overall, U.S. incentives can tilt the economics, but they do not fully close the gap in cost or manufacturing breadth.
Finally, it’s essential for companies to balance the pursuit of lower costs with maintaining quality. Whether producing in China or elsewhere, strong quality control is non-negotiable. Industry experts stress that the benefits of manufacturing in China (or any country) will only materialize if the supply chain is managed correctly. For example, one supplier guide recommends a three-step approach to ensure high-quality output: conduct detailed factory audits, provide crystal-clear product specifications, and enforce ongoing quality control inspections. This rigorous approach helps catch defects early and keeps production on target. Firms that simply chase the lowest prices without oversight often suffer from inconsistencies or recalls.
In practice, companies should invest in robust quality assurance regardless of location: hire inspectors or third-party auditors, use real-time monitoring, and maintain close communication with the factory. In China specifically, many factories already expect foreign buyers to perform such audits and testing. Outside China, it’s equally important to develop local QA teams or partnerships. In other words, cost reductions should never come at the expense of product standards. By insisting on thorough QC processes everywhere, companies can help ensure that diversifying away from China doesn’t lead to quality drops. Balancing cost and quality often means accepting slightly higher prices at a reliable supplier than facing the hidden costs of poor quality or delays.
Summary of Key Points: In recent years the U.S. and China have imposed large tariffs on each other’s goods, dramatically altering trade flows. These tariffs have raised costs for importing manufacturers and prompted global supply-chain shifts. Nevertheless, China’s manufacturing sector remains strong. It accounts for roughly one-third of world output and offers unique advantages: a massive integrated supply chain, advanced infrastructure and a skilled workforce. Chinese factories have also moved up-market, producing high-tech and high-quality products for global brands. While tariffs make Chinese exports more expensive in the U.S., China is offsetting this through automation, domestic demand stimulation and overseas expansion. In contrast, other manufacturing hubs (e.g. Vietnam, India, Mexico) can offer lower wages or proximity to U.S. markets, but they still lack China’s full ecosystem. In summary, tariffs have added costs and complexity, but they have not nullified the benefits of China’s manufacturing prowess.
The Future of Manufacturing Amid Tariff Changes: Looking ahead, businesses must stay agile. Tariff policies could continue to change with political dynamics, so companies should build flexible supply chains. Best practices include diversifying sourcing (the “China+1” strategy), strengthening inventory and logistics resilience, and continuing to invest in China’s industrial partners for as long as it makes sense. Chinese manufacturers, for their part, are likely to keep investing in R&D and automation to maintain a competitive edge. Firms working with Chinese suppliers should emphasize clear specifications and frequent quality checks (audits, samples) to ensure standards are met. At the same time, companies evaluating non-China locations should weigh total cost – including logistics and quality assurance – not just wages. In short, the key is to balance cost, quality and risk: use China where its advantages outweigh tariffs, and use alternatives to hedge or serve local markets.
We encourage manufacturers, procurement managers and prototyping firms to review their current sourcing strategies in light of these changes. Assess your exposure to tariffs by analyzing which products come from China and consider opportunities to diversify supply or negotiate new terms. Evaluate the trade-offs: would a slightly higher cost in Vietnam or India still yield the best overall value? Consult with industry experts like WJ Prototypes or supply-chain analysts to model the impacts on your specific products. By proactively planning for tariffs – for example, by securing key components now or qualifying backup suppliers – businesses can turn uncertainty into competitive advantage.
Additional Resources: For readers interested in deeper analysis, the following reports and articles are recommended:
Contact Information for Professional Consultation: If your company needs tailored advice on Prototyping, 3D Printing, Custom parts manufacturing and tariff strategies, our team is here to help. You can reach our manufacturing and engineering specialists at info@wjprototypes.com or call +86-189-2523-4131. We offer manufacturing and prototyping solutions for industries from electronics and automotive to aerospace, and we can work with you to devise the most cost-effective, high-quality manufacturing plan in the current tariff environment. Feel free to reach out for a one-on-one discussion of your unique challenges and opportunities.
Overcome the tariff changes with expert help. Contact us through our contact us page
OR Email to info@wjprototypes.com